What Utilities do I need? This is always one of the most important questions a plant builder will receive and a customer trying to determine the costs of operation. The Utilities are important to determine once the plant is designed and engineered to determine what utilities are required and what sizing is needed to maintain the operation of the plant. It always comes back to what utilities do I need?
Boilers
Maintaining a biomass boiler is essential to ensure its efficiency, safety, and longevity. Biomass systems play an important role in sustainable energy solutions by converting organic materials into heat. Like any other complex machine. Its optimal functioning depends on regular, specific maintenance.
Understanding the basics of biomass boiler operation is key. It can help prevent costly downtime and keep the system running smoothly. It also helps with the maintenance the system needs. This article will cover the basics of maintaining your biomass boiler. It will discuss daily, weekly, monthly, and yearly tasks. It will also address common issues and decide when to seek professional help. By sticking to a regular maintenance program, you can greatly improve your boiler’s performance. This will cut costs and make the boiler last longer. So, it’s a wise investment for any business that relies on biomass energy.
Daily and Weekly Maintenance Tasks
Daily and weekly maintenance of your biomass boiler involves routine inspections and minor cleaning tasks to ensure the system is running smoothly. These ongoing activities are critical for the early detection of problems and for maintaining operational efficiency.
Monthly and Annual Maintenance Routines
Monthly and annual maintenance routines are critical to the long-term health and performance of your biomass boiler. These tasks go beyond daily and weekly inspections and involve more detailed checks and adjustments.
Common Problems and Solutions
Despite regular maintenance, biomass boilers can still experience operational problems. Understanding common problems and their solutions can help you resolve them promptly and maintain efficient operations.
The Impact of Maintenance on Boiler Efficiency
Regular maintenance has a profound effect on the efficiency of a biomass boiler. Ongoing maintenance not only ensures optimum performance but also plays a vital role in saving energy and reducing costs.
Professional Services & DIY Maintenance
When it comes to biomass boiler maintenance, choosing between professional service and DIY tasks can be challenging. Both approaches have their benefits, and understanding them can help you make an informed decision.
Boilers Conclusion
Regular maintenance is essential for optimal performance and longevity of your biomass boiler. By following daily, weekly, monthly, and annual maintenance routines, you can avoid costly repairs, improve efficiency, and extend the life of your equipment. Investing in professional services for complex tasks ensures thorough inspections and expert treatment, while routine inspections and minor repairs can be managed in-house. In addition, long-term maintenance programs and strategic upgrades can future-proof your biomass boiler to keep it in line with the environment, adopting the latest technological advances and sustainability goals.
As a full-service boiler system solutions provider that integrates boiler design, boiler manufacturing, boiler installation, and boiler maintenance, PEUSA provides professional service and support to ensure that your boiler system operates at its best. By working with PEUSA, you can develop and implement a comprehensive regular maintenance program to ensure your biomass boiler runs efficiently and reliably, providing your business with a sustainable and cost-effective energy solution. In short, consistent and proactive maintenance is essential to maximize the benefits of biomass energy, and professional services will help you achieve this.
Chillers
A chiller is a machine that removes heat from a liquid via a vapor-compression or absorption refrigeration cycle. This liquid can then be circulated through a heat exchanger to cool equipment, or another process stream (such as air or process water). As a necessary by-product, refrigeration creates waste heat that must be exhausted for ambiance, or greater efficiency, recovered for heating purposes. This is why it questions what utilities do I need?
Air Compressors
An air compressor is a device that converts power (using an electric motor, diesel or gasoline engine, etc.) into potential energy stored in pressurized air (i.e., compressed air). By one of several methods, an air compressor forces more and more air into a storage tank, increasing the pressure. When tank pressure reaches its engineered upper limit, the air compressor shuts off. The compressed air, then, is held in the tank until called into use. The energy contained in the compressed air can be used for various applications, utilizing the kinetic energy of the air as it is released and the tank depressurizes. When tank pressure reaches its lower limit, the air compressor turns on again and re-pressurizes the tank. This questions always what utilities do I need?
What utilities do I need? Nitrogen Generators are usually needed.
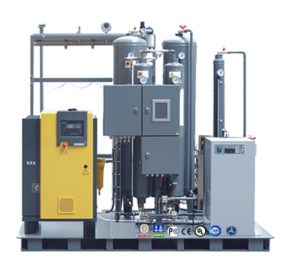
The technology of air-to-nitrogen production with adsorption processes in nitrogen generators is well-studied and widely applied at industrial facilities to recover high-purity nitrogen.
The operating principle of a nitrogen generator utilizing the adsorption technology is based upon the dependence of the adsorption rates featured by various gas mixture components upon pressure and temperature factors. Among nitrogen adsorption plants of various types, pressure swing adsorption (PSA) plants have found the broadest application worldwide.
The system’s design is based on the regulation of gas adsorption and adsorbent regeneration using changing pressures in two adsorber–absorbent–containing vessels. This process requires constant temperature, close to ambient. With this process, nitrogen is produced by the plant at the above-atmospheric pressure, while the adsorbent regeneration is accomplished at below-atmospheric pressure.
The swing adsorption process in each of the two adsorbers consists of two stages running for a few minutes. At the adsorption stage oxygen, H2O and CO2 molecules diffuse into the pore structure of the adsorbent whilst the nitrogen molecules are allowed to travel through the adsorber–adsorbent-containing vessel. At the regeneration stage the adsorbed components are released from the adsorbent vented into the atmosphere. The process is then multiplely repeated.
Advantages
High nitrogen purity: PSA nitrogen generator plants allow the production of high-purity nitrogen from air, which membrane systems are unable to provide – up to 99.9995% nitrogen. But in most cases, they do not produce more than 98.8% nitrogen with the remainder being argon that is not separated from the nitrogen by the usual PSA process. The argon is not normally a problem, as argon is more inert than nitrogen. This nitrogen purity may also be ensured by cryogenic systems, but they are considerably more complex and justified only by large consumption volumes. The nitrogen generators use CMS (carbon molecular sieve) technology to produce a continuous supply of ultra-high purity nitrogen and are available with internal compressors or without.
Low operating costs: By substitution of out-of-date air separation plants nitrogen production savings largely exceed 50%. The net cost of nitrogen produced by nitrogen generators is significantly less than the cost of bottled or liquefied nitrogen.
Environmental impact: Generating nitrogen gas is a sustainable, environmentally friendly, and energy-efficient approach to providing pure, clean, dry nitrogen gas. Compared to the energy needed for a cryogenic air separation plant and the energy needed to transport the liquid nitrogen from the plant to the facility, generated nitrogen consumes less energy and creates far fewer greenhouse gases.